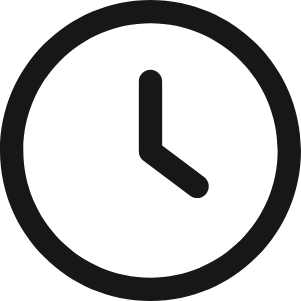
The industrial automation sector is witnessing substantial growth, fuelled by advancements in deep learning and artificial intelligence (AI). Key trends shaping the future of this industry include the integration of robotic process automation (RPA) and AI-driven predictive maintenance, both of which significantly enhance operational efficiency and flexibility. Furthermore, the emergence of smart factories, underpinned by […]
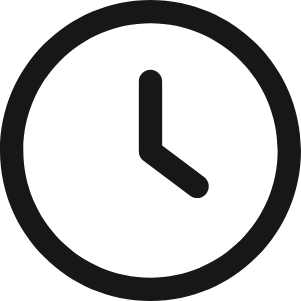
In an era where precision, efficiency, and adaptability drive industrial innovation, 3D imaging has emerged as a cornerstone technology. From quality control to advanced robotics, the integration of 3D camera solutions is revolutionizing operations across various sectors. JM Vistec System, a leader in industrial imaging solutions, offers state-of-the-art 3D camera systems tailored to meet the […]
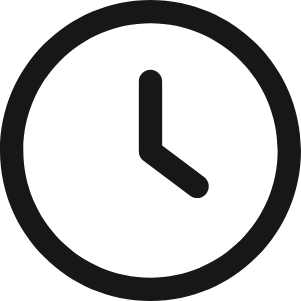
Schneider-Kreuznach is a globally recognized manufacturer of high-performance optics, renowned for its dedication to precision and durability. With decades of expertise, the company has established itself as a trusted leader in optical technology. Schneider-Kreuznach’s extensive range of industrial lenses delivers unparalleled quality for machine vision applications, meeting the specific demands of industries worldwide. Precision-Engineered Lens […]
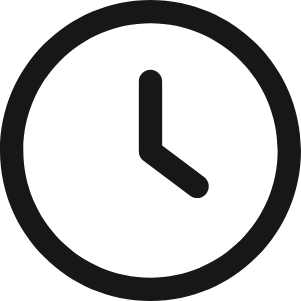
Machine vision systems play a pivotal role in various industries, from manufacturing to logistics. These systems are tasked with ensuring accuracy, consistency, and speed in inspecting products, parts, and materials. One of the critical factors that can make or break the efficiency of these systems is the quality of lighting. This is where Smart Vision […]
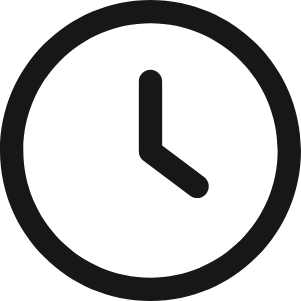
SVS-VISTEK cameras are an excellent choice for industries that require clear, high-quality images and reliable performance. These cameras stand out in precision manufacturing due to their exceptional accuracy and high-resolution capabilities. Equipped with the latest sensors, SVS-VISTEK cameras deliver ultra-high megapixel resolution, enabling detailed inspections and precise measurements. This clarity is crucial for detecting even […]
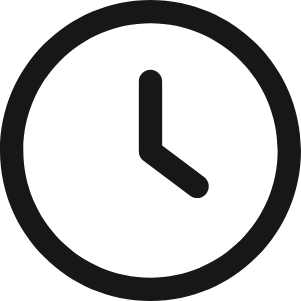
What is Neurocle Neurocle is a pioneering company that provides deep learning vision software aimed at non-experts, with the goal of making this advanced technology a norm in diverse fields such as manufacturing, medical, and logistics. As experts in computer vision and deep learning, Neurocle is driven by the vision of making deep learning vision […]
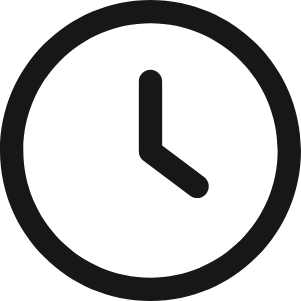
In the fast-paced world of machine vision, capturing high-quality images is essential. Opto Engineering, a leader in advanced optical components, offers a variety of lenses tailored to meet the needs of different applications. This article will explore two specific lens types offered by Opto Engineering—telecentric and 360° lenses. We’ll look at their characteristics, benefits, and […]
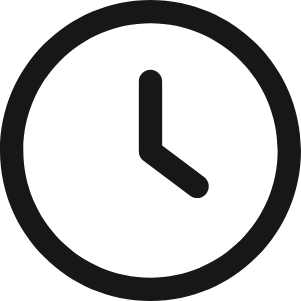
Introduction to Opto Engineering Opto Engineering is well-known for its expertise in optical engineering and its dedication to providing high-quality optical solutions. They offer a wide range of products, including lenses, lighting systems, and cameras, all designed to improve image quality and performance in machine vision applications. Opto Engineering’s innovative designs and precision make them a […]
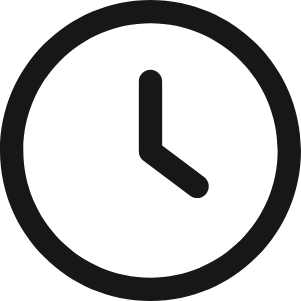
In the world of industrial automation, vision inspection systems play a crucial role in ensuring product quality and operational efficiency. These systems use advanced cameras, lighting, and image processing software to detect defects, measure dimensions, and guide robots in various manufacturing processes. Industrial cameras are at the heart of these systems, capturing high-resolution images that […]
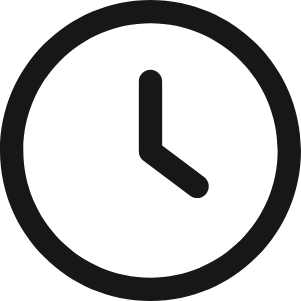
In the realm of industrial automation, choosing the right vision system is crucial for optimising production efficiency and quality control. Two primary types of vision systems dominate the market: fixed industrial scanners and smart sensors/cameras. Each has unique features and applications, making them suitable for different industrial needs. This article explores the differences between these […]
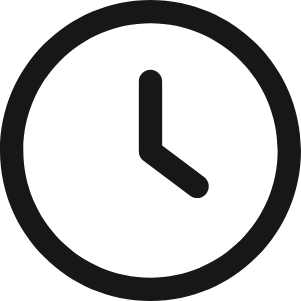
SWITCH is organised by Enterprise Singapore (ESG) and supported by the National Research Foundation (NRF). It features various innovation and partner programmes culminating in an exciting hybrid festival featuring conferences.
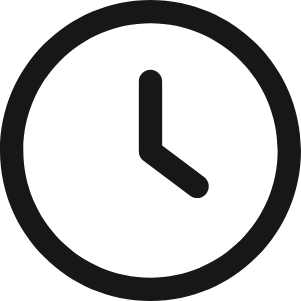
During the 2nd day of the 2019 Hannover Messe event, JM Vistec System was been interview by “Hello Singapore (狮城有约)” program and to be broadcast on Channel 8 soon. The interview will be focusing on JM Vistec System’s technology and capabilities, highlighting our 3D image processing software featuring the Fringe projection and Deflectometry setup. […]
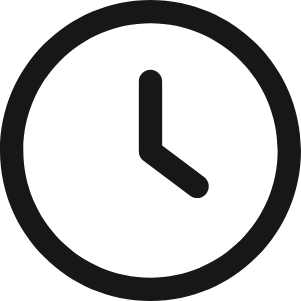
we are pleased to share that we are featured on Singapore Manufacturing Federation’s SMEC@SMF Connect which is a media publication platform by SMF themselves, featuring information from various industries and articles that are beneficial to the readers. We are truly humbled by the feature of our success story on our 3D Fringe Projection, and we hope […]
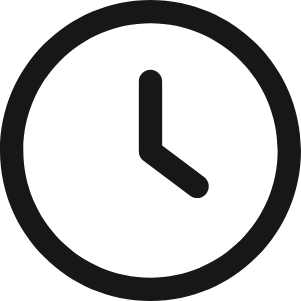
ITAP 2021 has been an exquisite 3 days’ worth of meaningful experience as 𝐉𝐌 𝐕𝐢𝐬𝐭𝐞𝐜 𝐒𝐲𝐬𝐭𝐞𝐦 𝐱 Hexagon Manufacturing Intelligence collaborated to bring smart factory solution in promoting diversity and inclusion. The agenda of this collaboration in conjunction of industrial 4.0 which broadens the range of resources. We aim to provide a well-rounded experience for our customers. […]
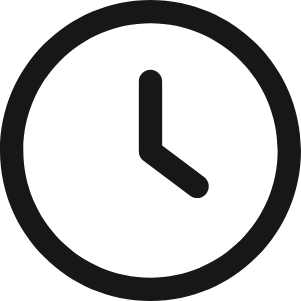
It’s evident that in this new world, technology is not a choice, but a fundamental business strategy that how the enterprise creates value today and in the future. https://lnkd.in/gsfc8V2F
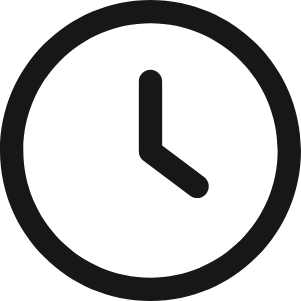
We are delighted to announce that JM VISTEC SYSTEM PTE LTD is presented the Go Global Awards 2021 for Top Place Professional Services on 14th October 2021. The International Trade Council’s Go Global Awards offer the opportunity to be recognized and honoured by their peers it also goes beyond winning trophies and citations. The program […]
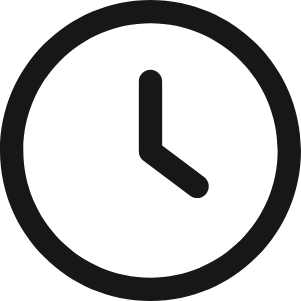
In October 2021, JMVS’s representatives Eugene Goh and Bing Kian managed to participate VISION World’s Leading trade fair for machine vision in Messe Stuttgart, Germany. We are filled with gratitude for the opportunity to able to meet our partners and friends at the trade shows especially during the pandemic. The event was astonishing, enabling us to be in […]
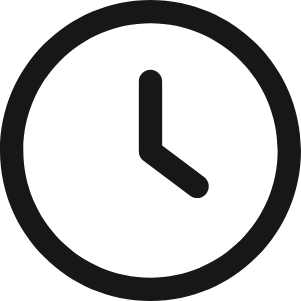
Today marks the 17th year of our company’s birth and we truly appreciate all our staffs for their hard work and dedication to JM Vistec System. Cheers to more milestones set together!
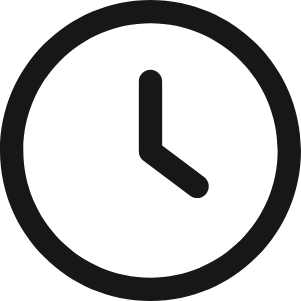
The inaugural Singapore-Chongqing Smart Manufacturing Business Networking Event took place on 25 August. Co-organised by A*STAR Collaborative Commerce Marketplace (ACCM), Singapore Manufacturing Federation (SMF), Chongqing Science and Technology Bureau (CSTB) and their partners, the hybrid event was attended by approximately 80 participants, and catalysed connections for 90 Singapore and 30 Chong Qing companies. JM Vistec […]
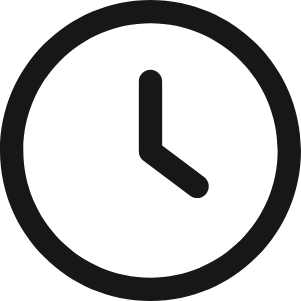
The Smart China Expo (SCE) 2021 is held on 23-25 August 2021 under the theme of “Smart Technology: Empowering Economy, Enriching Life”. The events follows the national development strategies, industrial development trends and major decisions and plans of the Chongqing Municipal Government and the CPC Chongqing Municipal Committee to focus on key areas including industrial […]
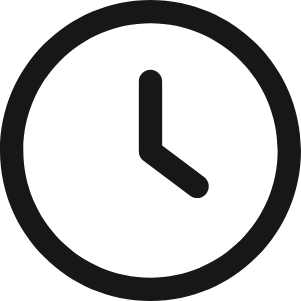
JM Vistec is very pleased to announce that we are the distributor for Opto GmbH in Singapore. Opto GmbH with more than 40 years of experiences in developing optical solutions for advanced imaging applications. Which have refined an extensive knowledge of what optics can do. This knowledge enables to deliver highly efficient optical solutions that balance economy […]
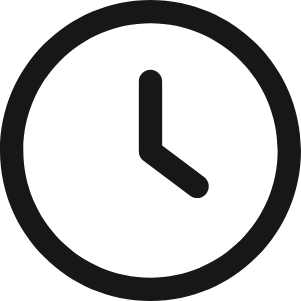
With the growing need for enhanced productivity, the effective adoption of automated optical inspection technologies together with relevant skilled manpower is essential. SIMTech has combined automation and intelligence to build up competencies in inspection modules and equipment for electronics, semiconductor, optics, and automotive industries. This webinar aims to help companies develop their internal competencies so […]
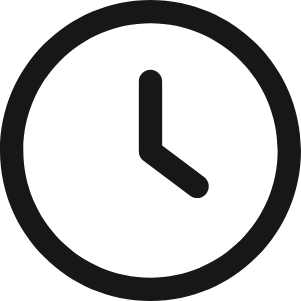
Ms Charlotte, Ms Rashidah, Dr ChengFang and Dr Malcolm for hosting the webinar. We are honoured to be given this opportunity to share our collaboration experiences with SIMTech and ARTC in such a meaningful event. Thank you for your participance and hope that this webinar was an enriching one to all attendees.
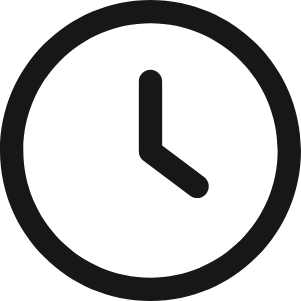
Thank you Singapore Manufacturing Federation for featuring us in your CONNECT magazine! As the leading machine vision specialist, JM VisTec System pride ourselves as the true blue Singaporean brand. Our core values are reflected by our national identity; Competitive Quality, Performance Driven and Service Assurance in technology capabilities. Our greatest appreciation goes out to all supporting partners […]
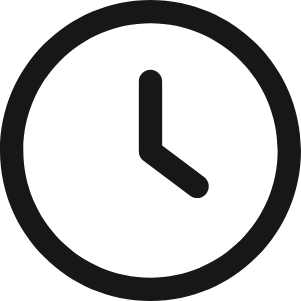
Great News!!! The China Vision Show 2021 was smooth-sailing and a successful one, thanks to the active participation of each and every one of you, as well as the unwavering support from our suppliers. JM Vistec System is very honored to showcase our high-quality products, services and one-stop visual solutions. Our team members were well-versed […]
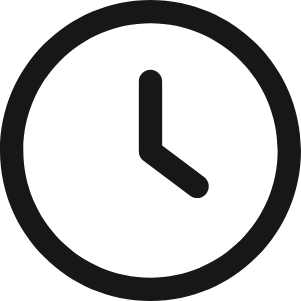
JM VisTec System has always believed that continuous learning can help us provide top-quality services to our clients. We play the important role of professionally delivering product information from our exclusive partners and establishing a mutually trusting relationship with clients to bring about a win-win situation. Attached photos show our rotating training on Saturdays. Our […]
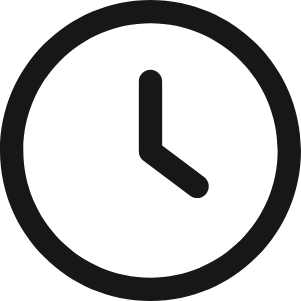
This is a milestone event for JM VisTec. We would like to express our sincere gratitude to Prof Tan Sze Wee, Mr Ho Yew Wee, Dr Xi Weiya, Dr Wong Chow Cher, Dr Wang Wei, Mr Chang Thai Nam, Dr Cheng Fang, Dr Zhang Jie and Ms Angeline Chang for taking time to pay us […]